When trying to develop soft silicone robots, we realized that we needed new methods for casting silicone shapes. As we got deeper into trying different casting methods, we thought: why not just build fully wax molds? But the bigger we wanted to make them, the more difficult they were to 3D print. In comes the idea: what if we used wax-dipped paper as a way to support large wax molds?
We started experimenting with a laser cutter and lots of wax.
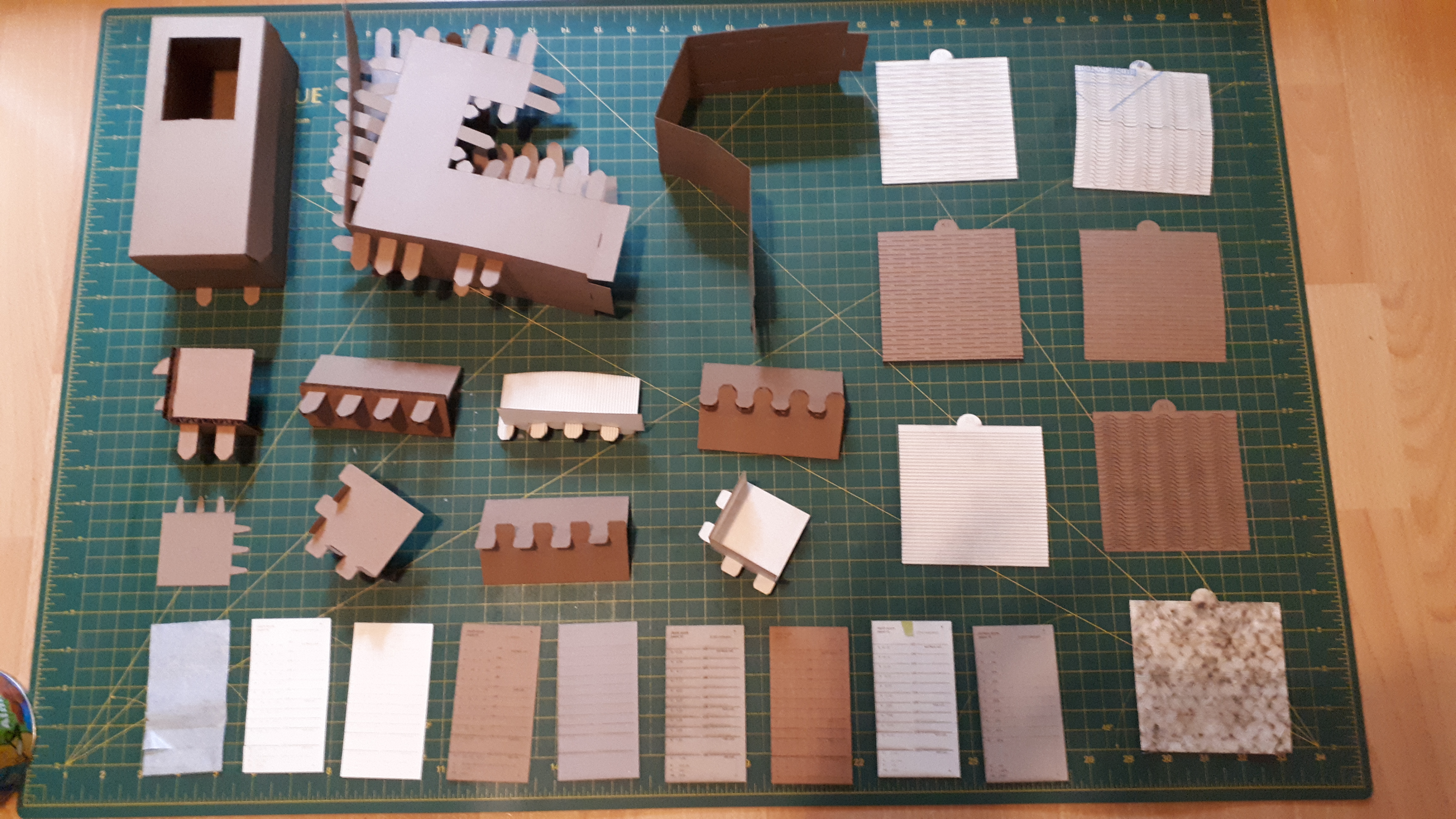
After a lot of hand-building, experimentation, and coding we ended up creating a system that went from 3D model to lasercut assembly pattern.

The system automatically calculated the kind of pattern based on the thickness of the paper you wanted to use, and the joins and holes between pieces of paper.
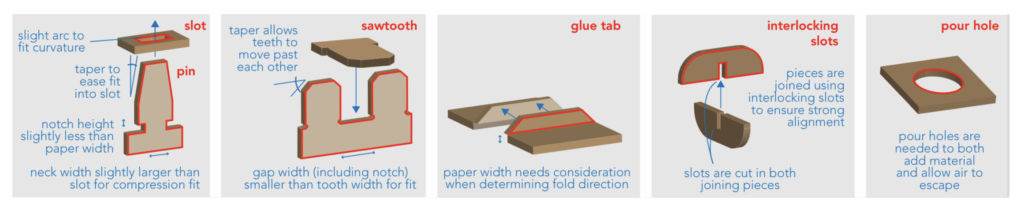
We made some cool shapes. One great one was a jello Bundt cake.
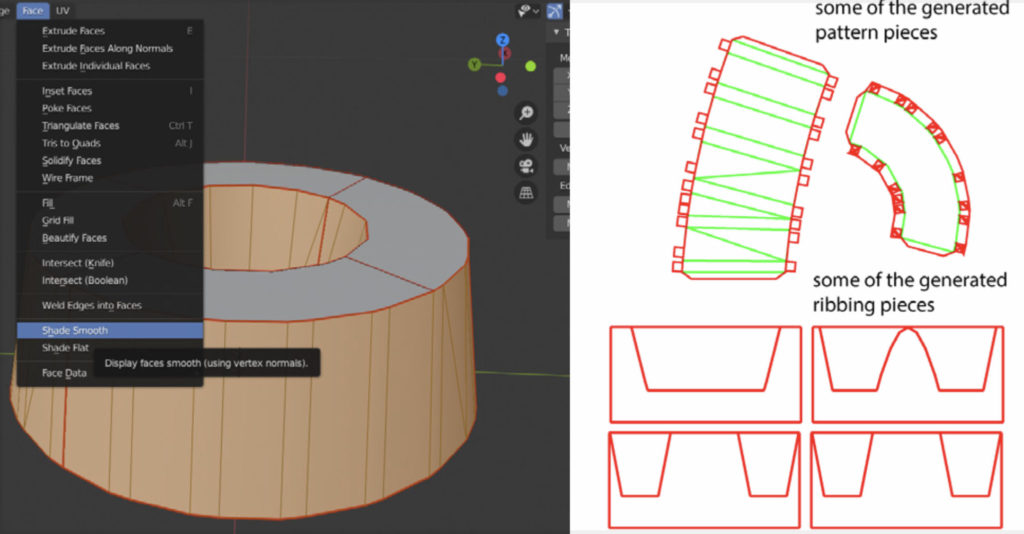
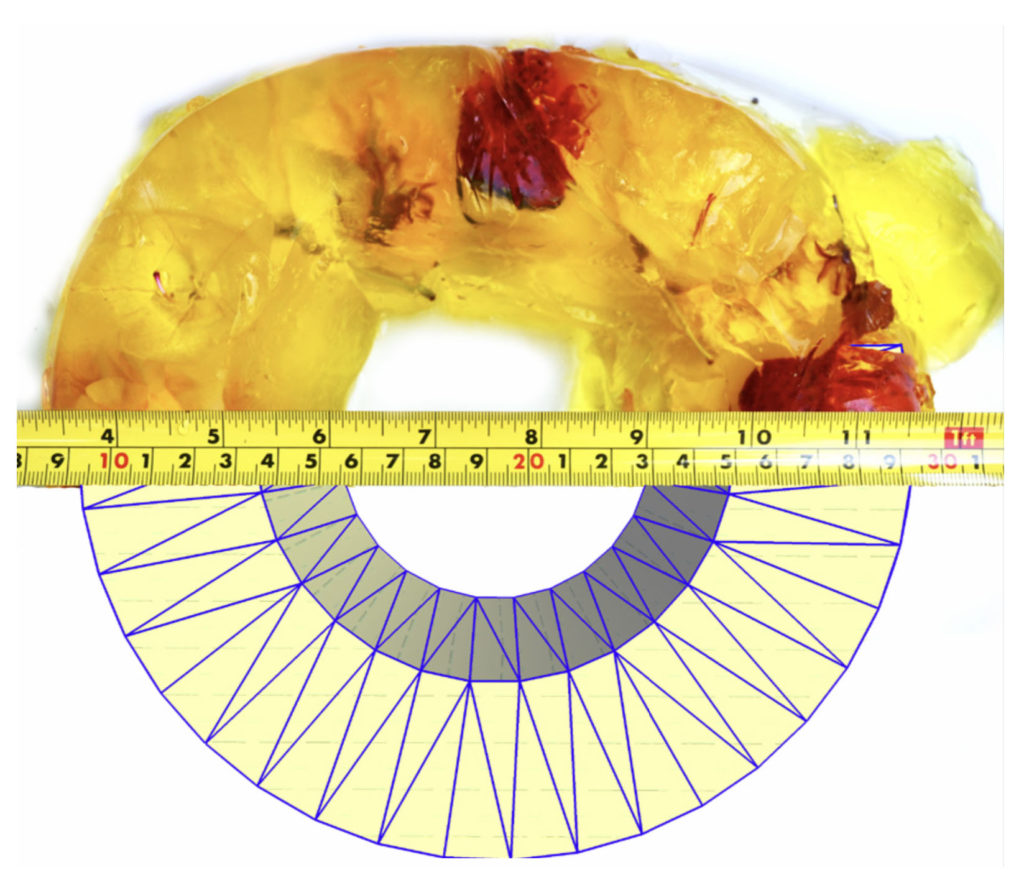
Or a plaster model of something like a sewing machine.
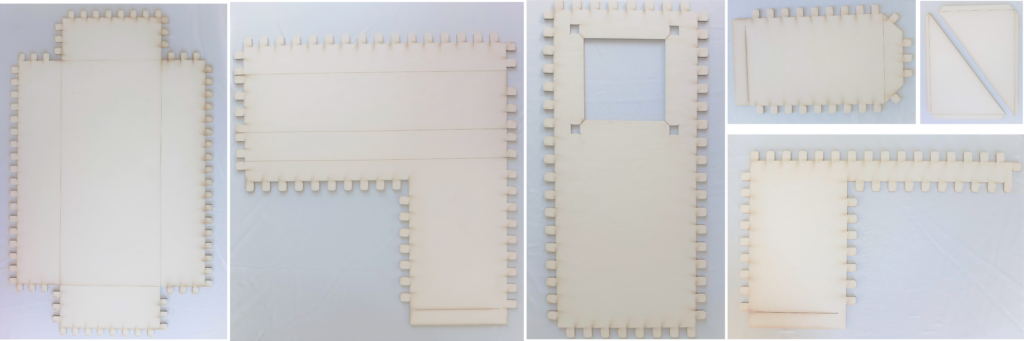
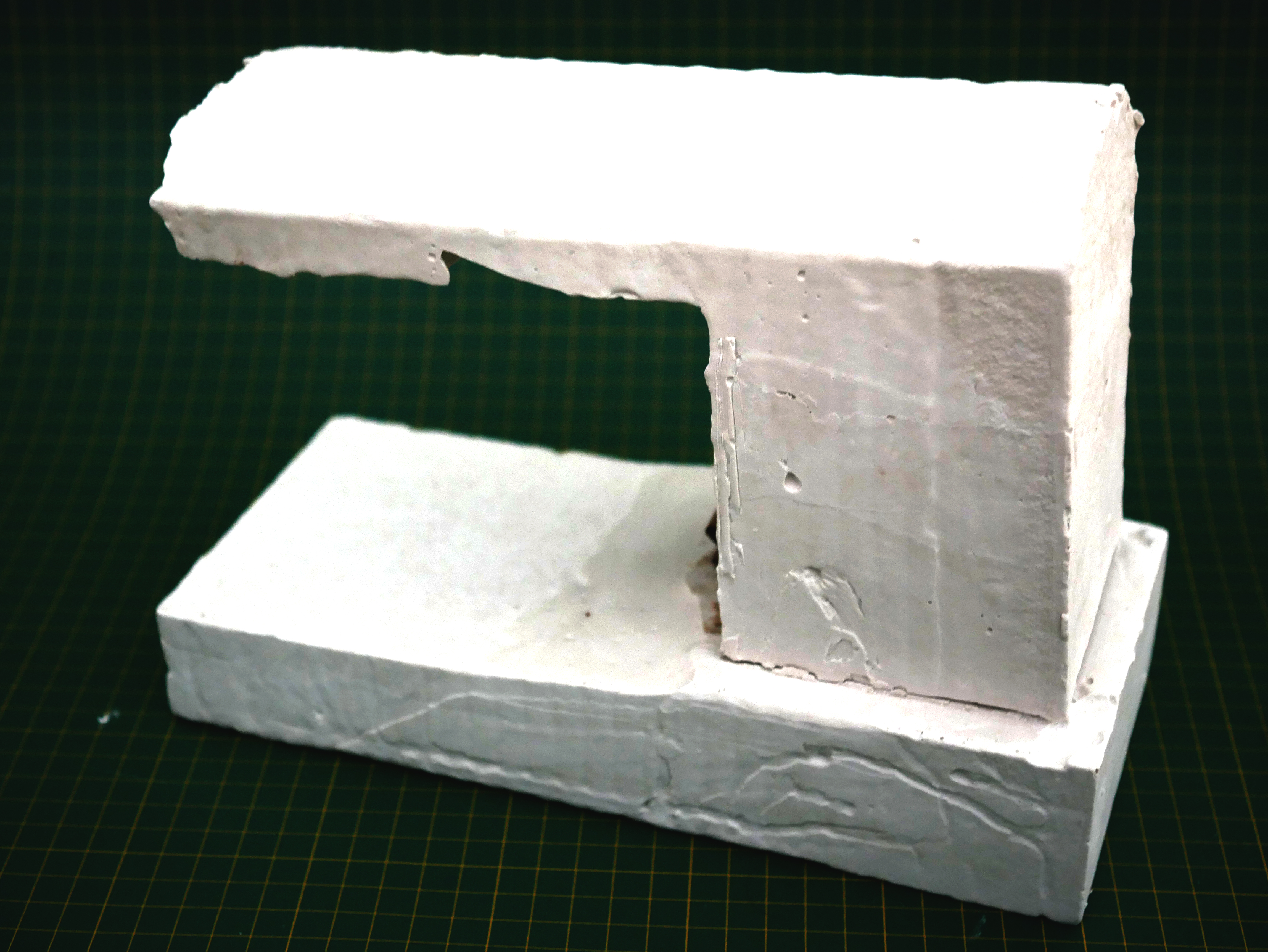